Accurate diagnostics lead to informed decision making & immediate rectification
The vibration data captured is processed using a dynamic range of analysis and post-processing tools in the Acoem Nesti4.0 predictive maintenance software platform, including:
- Advanced vibration indicators
- Calculations covering historical data
- Concatenated spectra
- 3D spectra
- Shock Finder filter.
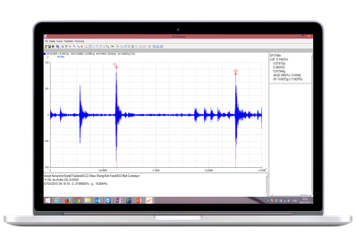
Acoem Eagle monitoring critical machinery
The pumps’ data collected in combination with Accurex™ AI automatic diagnostics proved the existence of structural resonance issues affecting the pumps.
The data identified that there was significant pipe stress from the solid outlet pipe, so the component was replaced with a flexible pipe. There was also twisting in the machinery’s frame during the bolting down procedure as part of the installation process. As these pumps are replaced seasonally, it was important that bolting down was performed correctly each time to withstand stresses.
The Eagle sensors take measurements on an ongoing basis to ensure that there are no stresses in place, while a complementary Falcon portable monitor system is used to take additional root-based vibration measurements for analysis of possible faults in other areas of the pump.
According to Mathew Smart, Acoem Australasia Industrial Reliability Solutions Manager, the Eagle not only pinpointed the exact problem the customer was facing, but also provides ongoing monitoring and data analysis to ensure that the situation doesn’t flare up again.