Challenges in Crane Condition Monitoring
Heavy loads, long periods of use, and a wide variety of facility conditions – cranes must perform at their best.Their critical nature to operations and complexity to repair, often requiring specialized labor and parts, makes crane or hoist condition monitoring a necessary component of successful predictive maintenance programs.However, optimizing crane performance through condition monitoring comes with its share of challenges.
Although vibration analysis has been around since the 1950s, its implementation into the monitoring and diagnostic of overhead cranes has been limited due to inherent problems associated with collecting the vibration data on these systems. Each crane application has its unique challenge to overcome with regards to the implementation of condition monitoring, but all cranes inherently have the same fundamental challenges in regards to proper vibration analysis data collection for condition monitoring and diagnostic purposes:
- Complex operating environment and limited access
- Variable Speed and Variable Load issues
- Maintenance difficulties due to height and restricted spaces
- Limited accessibility for equipment health diagnosis
- Remote monitoring in large port areas
- Implementation of real-time monitoring systems and reliable communication
- Determining optimal locations for accurate condition monitoring
Overcoming Challenges with Real Time Online Condition Monitoring Connected Solutions
As computer processing, data storage capabilities, and wireless communication technologies continue to advance, the landscape of continuous vibration monitoring systems undergoes constant change. The implementation of these technologies on cranes has been limited in the past but is now on the rise due to the growing focus on reliability goals and asset management through condition monitoring practices. When considering crane-specific applications, it becomes crucial for end-users to carefully assess and determine the most suitable continuous monitoring program that aligns with their specific requirements, as not all monitoring systems are identical.
By embracing these advanced techniques, industries can proactively identify problems at an early stage, optimize maintenance strategies, and significantly enhance overall crane efficiency. Join us on this exploration as we delve into how continuous online monitoring and real-time analysis are revolutionizing crane operations, fostering increased productivity and achieving remarkable success.
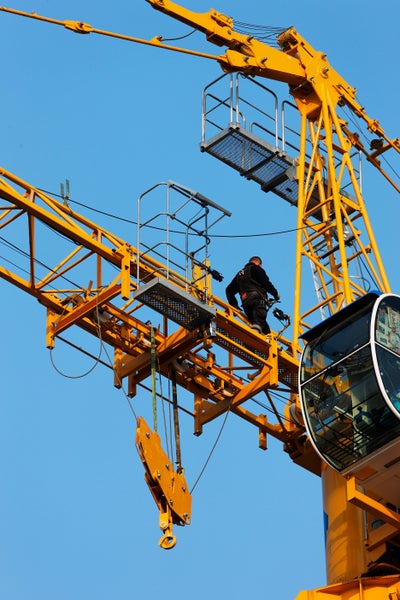
Early Fault Detection: Proactive Prevention of Potential Issues
- Real Time Online Condition Monitoring swiftly identifies emerging problems in crane components such as hoists, motors, gears, brakes, and cables.
- By catching faults at an early stage, proactive maintenance can be scheduled, preventing catastrophic failures and minimizing downtime.
Proactive Maintenance Scheduling: Empowering Reliability
- Online condition monitoring, with real-time data analysis, facilitates the implementation of proactive maintenance strategies.
- Anticipating failures becomes possible, enabling optimized schedules and reducing breakdowns, resulting in increased equipment reliability.
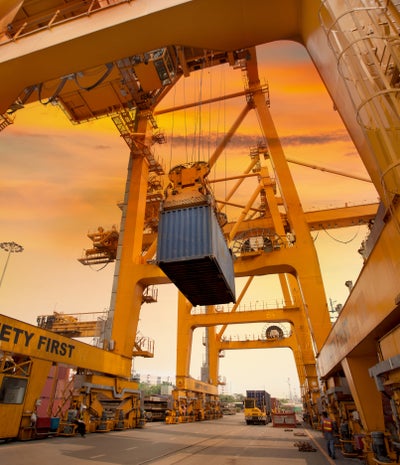
Extended Equipment Lifespan: Ensuring Longevity
- Regular monitoring of crane components enables the early detection of wear and tear.
- Timely maintenance or replacement can be conducted, extending the lifespan of the equipment.
Cost Minimization: Mitigating Expenses
- Reactive maintenance is costly, involving emergency repairs, component replacements, and potential production losses.
- By embracing condition monitoring, proactive measures can be taken, reducing expenses and optimizing maintenance costs.
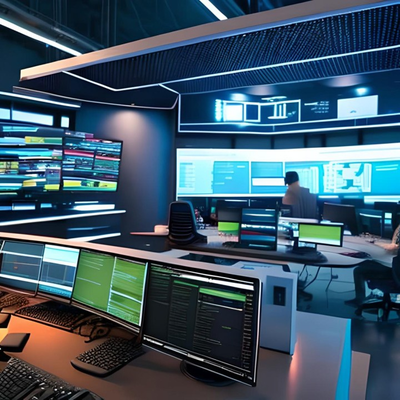
Remote Monitoring: Unleashing Efficiency
- Centralized monitoring systems grant real-time remote access to data.
- Multiple cranes can be monitored simultaneously, enhancing operational efficiency and reducing physical constraints.
Real time Insights with Edge Computing: Staying Ahead of the Game
- Automated alerts and notifications promptly inform maintenance personnel of abnormal readings or impending issues.
- Proactive measures can be taken in a timely manner, ensuring seamless crane operations.
The advancements in technology have opened up numerous options for monitoring machine condition, making it feasible to develop and implement monitoring systems for critical crane applications. The success of any technology-based monitoring program for cranes relies on the end-user’s system expectations, the specific crane being monitored, and the budgetary constraints that shape available capital funds for the project. As technology continues to progress, its integration into industrial applications is only limited by one’s imagination. By leveraging condition monitoring, industries can harness the full potential of cranes, minimizing risks, and maximizing productivity.
Acoem Solutions
Tailored for Crane Monitoring
Acoem has developed a tailored approach to address the reliability challenges faced during Crane Monitoring. By conducting thorough audits, predicting equipment failures, and implementing sustainable solutions with advanced technologies, Acoem helps industries and ports improve their operations.
Our expert team has years of experience working on different industries with exposure to local working conditions. This specialist knowledge combined with many years of experience has led us to offer comprehensive solutions and diagnostic services remotely as well as on-site.
Next Generation Reliability Solutions
A suite of IOT-driven ecosystem
Our predictive maintenance tools, powered by AI and utilizing wired or wireless sensors, IoT, augmented mechanics, machine learning, and data analytics, help anticipate problems before they occur. Schedule maintenance at the right time, receive alerts for potential issues, and enhance industrial productivity with certainty.