What is Condition Monitoring?
Condition monitoring utilizes various technologies, sensors, and signal analysis to diagnose the health of rotating machinery and other equipment. It’s a proactive approach that prevents unexpected equipment failures, ensuring smooth operations. Accelerometers are the most common data signal-capturing sensors, while leak detection using Acoustic Infrared Cameras has become an industry standard, minimizing gas and air loss within industrial facilities. Additionally, Infrared Thermography is widely employed for routine monitoring of potential overheating issues in electrical cabinets. Using condition monitoring enables you to assess the current health, degradation, and any relevant changes to your machines, helping to avoid failures and eliminate unplanned downtime.
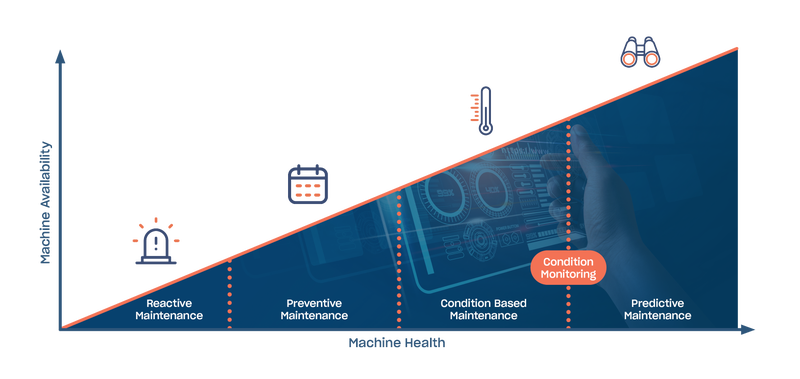
While state-of-the-art corrective measures are important, preventing vibration is equally crucial. Techniques like balancing unbalanced parts (fans, impellers) and laser shaft alignment ensure perfect alignment between components, minimizing friction and extending equipment lifespan.
The integration of the Internet of Things (IoT) and Artificial Intelligence (AI) has further enhanced CM, enabling real-time monitoring and more accurate predictive maintenance. This evolution has led to increased efficiency, reduced downtime, and extended equipment lifespan, making condition monitoring indispensable to modern industrial operations.
What Are the Types of Condition Monitoring?
Condition monitoring is crucial for both predictive and preventive maintenance strategies because of the performance data it collects and what that data reflects. Machine data is collected in different ways, depending on the type of machine being assessed. The below figure shows the four main condition monitoring techniques in use today.
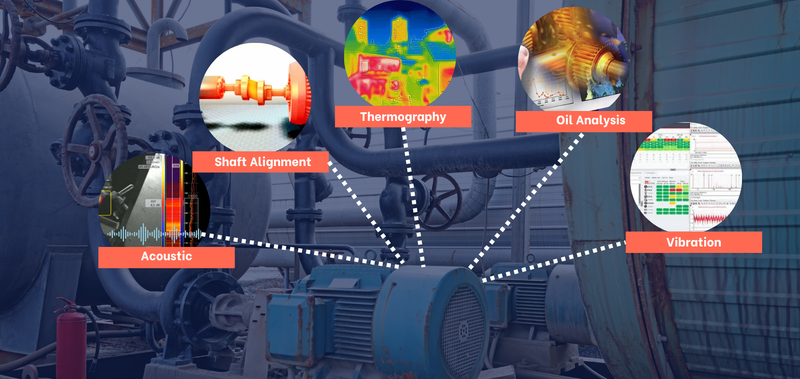
- Acoustic Emission:
All machines with rotating parts make sound – when that sound changes, you should look for faults. Detecting changes in high-frequency emissions can help catch faults early. Equipment with roller bearings, lack of lubrication, or bad seals can benefit from acoustic emission condition-based monitoring.
- Shaft Alignment:
Ensuring proper alignment of rotating shafts is critical to reducing wear and tear on machinery. Misalignment can cause excessive vibration and heat, leading to premature failure of components. Laser Shaft alignment solutions help maintain precise alignment, thus extending the lifespan of equipment and enhancing operational efficiency.
- Thermography:
With moving parts comes heat, and any change in temperature within a machine can indicate an issue. Monitoring for hot and cool spots helps prevent overworking a machine, thus preventing downtime. Thermography detects radiation in the form of heat coming off an object, similar to thermal imaging.
- Oil Analysis:
Machine lubricant or oil can contain debris, which can wear down your machine. Analyzing debris helps correct other machine faults before they become failures. Oil analysis is often used in motor vehicles to predict strange debris or particles before a problem arises.
- Vibration Analysis:
Rotating parts vibrate, and those vibrations can fluctuate. Using vibration analysis in predictive maintenance strategies alongside machine learning allows you to understand the exact patterns for each machine, enabling you to predict problems before they become faults.
Condition Monitoring in Early Days: Challenges and Limitations
In the early 2000s, the condition monitoring process was rudimentary and manual. Engineers relied on standard data collection methods, such as periodic inspections and manual measurements, to assess the health of machinery. Tools like handheld vibration analyzers and infrared thermometers were commonly used for data collection. While route-based data collection produced good results, the process was time-consuming, and signal quality was often restricted by hardware and storage limitations. Data analysis was typically carried out using desktop software installed on a single computer, constraining accessibility and slowing collaborative efforts.
Connectivity was also limited. Data had to be manually recorded and analyzed, often leading to delays in identifying potential issues. The lack of real-time monitoring meant many problems were only detected after significant wear or damage had occurred, resulting in unexpected downtime and higher maintenance costs. Despite these challenges, early practices laid the groundwork for the advanced, technology-driven CM techniques we use today.
The Rise of Online Condition Monitoring Systems
The evolution of condition monitoring in the early 2000s saw a significant shift from manual inspections and periodic data collection to advanced online systems. Early developments in sensor technology and data transmission laid the foundation for continuous, real-time monitoring. Modern systems use various sensors to gather data on vibration, temperature, and acoustics, which is then transmitted to centralized storage and analyzed using sophisticated software and machine learning algorithms.
These systems were connected to the client’s local area network (LAN), allowing data retrieval from a single computer. Server technology was basic, but rudimentary interfaces offered remote access through assigned IP addresses in the network. This early-stage access to configuration options laid the groundwork for more advanced features in the future. The benefits of online condition monitoring include real-time detection of anomalies, improved accuracy, and enhanced predictive maintenance capabilities, helping reduce downtime, extend equipment lifespan, and optimize maintenance strategies.
Transforming Condition Monitoring: Standardization, Mobility, and the Power of the Internet
Today, the seamless integration of various CM technologies has been achieved through standard protocols like Modbus, OPC, and MQTT. Browser-based dashboards, accessible from anywhere via the internet, empower plant managers to optimize facility operations for superior efficiency and reliability.
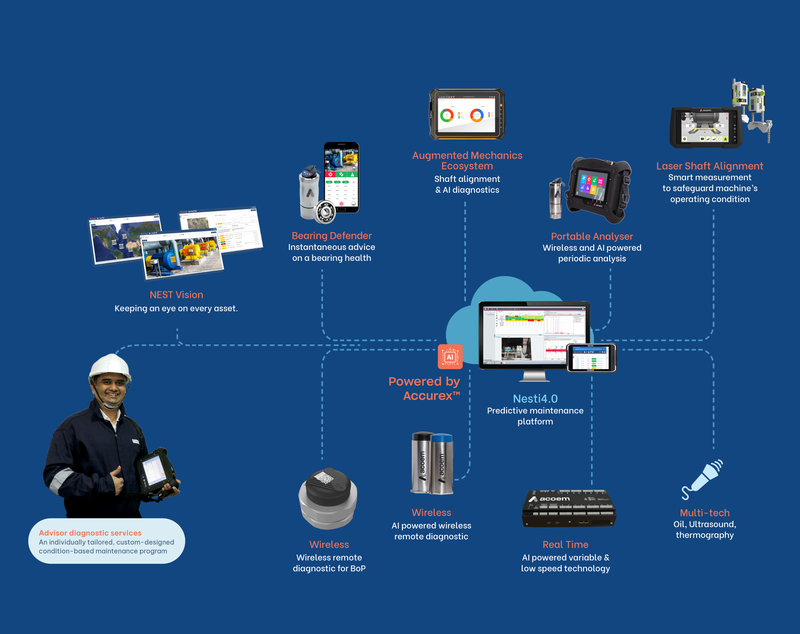
Seamless Installation: A Real-World Example
Imagine a young CM engineer in 2010, tasked with installing online monitoring systems for two hydro turbines in a remote area. Wiring the power supply and sensors was straightforward, and the on-site IT team ensured LAN connectivity to the systems. Wi-Fi was readily available on-site, and with an iPhone in hand, the engineer could verify sensor signals remotely while moving between the two turbine houses as the turbines were running and vibration signals started to float in.
Thanks to HTML interface websites stored on the firmware of the Online Monitoring System, accessible through the iPhone’s Safari browser via Wi-Fi, the job was smooth and easy, ensuring valid data integrity while checking the hardware, load conditions, and operating states. This glimpse into the future of CM showed how asset monitoring could become simpler, with signals visible on the screen and warnings and alarms displayed on the commissioning interface.
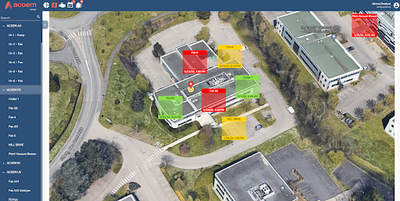
Revolutionizing Equipment Health Management with Modern Wireless Monitoring
Since those early stages, modern wireless monitoring systems have revolutionized how industries track and manage equipment health. Today, we can oversee machine conditions with beautifully designed interfaces accessible via any browser on all devices, such as tablets, phones, laptops, and computers. Leveraging wireless technologies such as Wi-Fi, Bluetooth, and cellular networks, these systems enable real-time data collection from remote or hard-to-reach locations. This transition from cumbersome interfaces to user-friendly mobile access highlights significant advancements in condition monitoring and asset management.
Modern accelerometers communicate wirelessly, eliminating the need for physical connections between the sensor and the data-capturing and processing unit. This allows for seamless transmission of signals to a gateway, where the data is integrated into a network database or the cloud. This capability enhances monitoring accuracy, reduces maintenance costs, and improves operational efficiency by providing instant access to critical equipment data from anywhere, at any time. As technology continues to advance, the integration of wireless monitoring solutions with IoT and cloud-based analytics promises even greater insights and proactive maintenance capabilities for industrial applications.
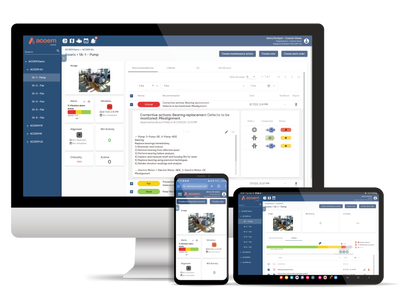
Beyond Today: The Vision of Acoem NEST for the Future
The future of condition monitoring is poised for significant advancements, driven by cutting-edge technologies such as IoT and AI. Wireless sensors and cloud-based data storage will enhance accessibility and reduce the need for manual data collection. Fast forward to 2024, with platforms like Acoem NEST Vision representing the cutting edge of asset management. Imagine the joy of our engineer, who no longer needs to navigate cryptic HTML interfaces!
The results from wireless sensors, portable data collectors, online monitoring systems, thermal cameras, oil analysis, and more can all be integrated into a single visually user-friendly platform. This data harvesting capability has revolutionized asset management, making it easier, more reliable, and more efficient to combine multiple resources, getting a holistic picture of a machine’s health.
By embracing these advancements in condition monitoring technologies, industries can gain a significant competitive edge through increased production efficiency and reduced downtime. The journey of condition monitoring has been remarkable, and its future holds even greater promise.