Vibration velocity is the basic indicator used to diagnose the health of rotating machineries.
Alert thresholds for each type of rotating equipment in ISO standard 10816 were in fact established based on the vibration velocity indicator. It could therefore be assumed that using a vibration meter to take regular vibration measurements would be sufficient to properly monitor a machine. Yet a machine can have an acceptable vibration velocity level without being in good health given that, using this indicator, certain defects only become detectable after a longer period of time. This applies in particular to defects on bearings which, as you will see in the example below, are essential components in the maintenance program of rotating machineries.
We were contacted by the maintenance staff of a water treatment plant regarding an issue with their pumps: the pumps were producing an unusual noise that was perceptible to the technicians, and though they suspected it was linked to a bearing, their vibrometer showed all bearings to be in the green. The client asked that we confirm his intuition with our FALCON vibration analyzer.
As shown in the image below, vibration levels were within acceptable range on all bearings and all 3 planes (axial, horizontal and vertical). However, our automatic diagnosis software AccurexTM detected a problem on the fourth bearing. The in-depth diagnosis confirmed an issue on that bearing with a confidence index of 100%. It recommended lubrication as a first measure, and replacing the bearing as soon as possible if the usual noise were to persist.
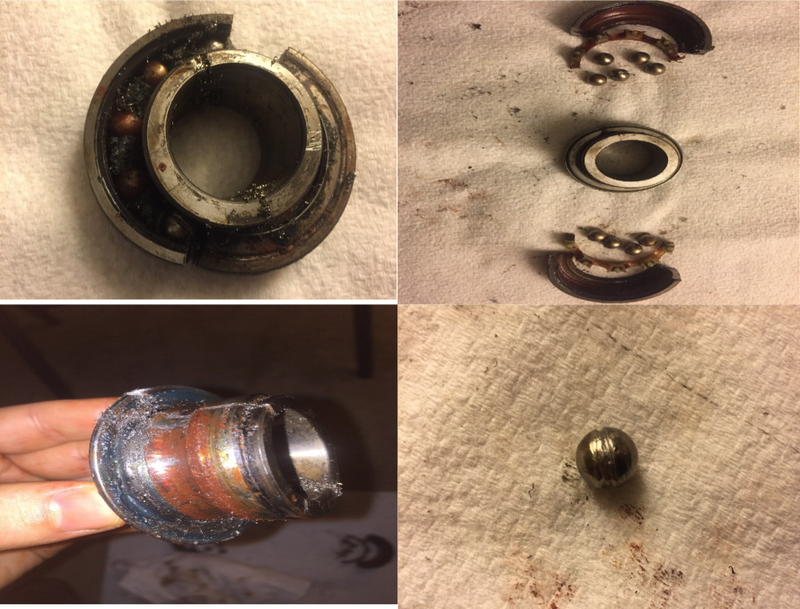
Vibration velocity readings from before (below, left) and after (below, right) the bearing was changed clearly demonstrate that although the overall vibration level was still within acceptable range, it was well above optimum performance levels.
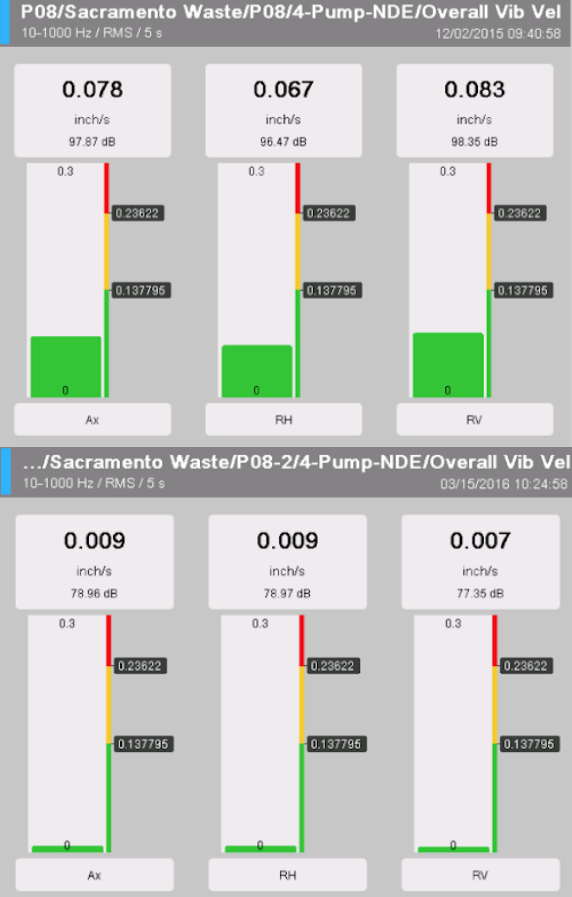
What conclusions should be drawn from this example? We found 3:
- a machine can display vibrations deemed acceptable by ISO standard 10816 and still have a defective component,
- based on vibration levels alone, a service technician could easily miss a significant defect and allow an unhealthy machine to keep running,
- even if the technician’s experience tells him there is a problem, without tool capable of analysing further, he cannot confirm his instinct; he could interpret action in the wrong way.
These conclusions substantiate the purpose of periodic monitoring tools capable of performing in-depth measurements and providing diagnostics. They allow for earlier detection of problems and significantly boost the health of rotating machineries: predictive conditional maintenance fully plays its role in optimizing process performance.