Cleaning the Air with Electrostatic Precipitators
An electrostatic precipitator is a filterless device that uses an electric charge to remove impurities from the air that are in solid, droplet, gaseous, or liquid form. It is an air pollution control device used for removing pollutants from smokestacks of factories, industrial manufacturing, and power plants.
Most industries use fossil fuels for their manufacturing processes, the result of which is the emission of smoke, which contains soot, ashes, and unburned CO2. Electrostatic precipitators (ESPs) take the soot, ashes, and unburned carbon dioxide from the smoke using an electric charge and release clean air or smoke into the atmosphere. Extraction of these harmful particles is important since they can cause harm to buildings, the environment, and people.
Though different areas of an industrial plant can operate in isolation, each piece of equipment has an impact on the other piece. You will be surprised to know that the performance of the boiler is largely dependent on the type of electrostatic precipitator in the plant. Particulate size and composition, temperature and volume of flue gas are dependent on the operation and maintenance of the combustion equipment. These two factors impact the ability of the industrial plant to comply with the air pollution limit stated by the Federal and state regulators.
Industries that Rely on ESPs
ESPs play a vital role in various industries where air purification is a priority. You’ll find these
- Cement plants
- Petroleum refineries
- Paper and pulp mills
- Fossil fuel-fired boilers
- Power generating stations
- Hazardous waste incinerators
- Municipal waste incinerators
- Lead/zinc/copper smelters
- Steel mills
Hunting Down Air Leaks: The Challenge
Imagine searching for tiny holes where air or gas is escaping from a system. Tracking these sounds helps us find the leaks. This is what air leak detection is all about, especially in electrostatic precipitators (ESPs), which are like air cleaners for factories.
As an Electrostatic Precipitator deals with more gas, it becomes less effective at catching bad stuff. Air leaks can pop up anywhere, making them hard to find. If you suspect there’s sneaky air in the ESP, check the O2 meter reading first. It’s smart to follow the plant’s rules since they often test for air leaks. When the device sucks in dust with negative pressure, air leaks can make the dust fly around. Air leaks also speed up the gas, so it stays less time inside the device. This can lead to issues like wetness and rust.
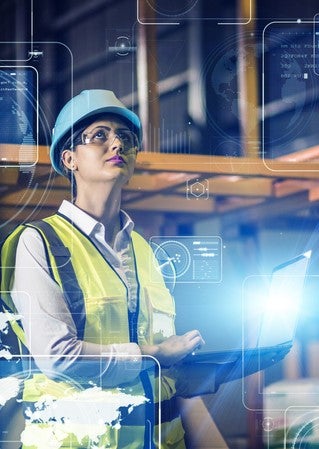
Challenges in Air Leak Detection
- Accessibility and Complexity: ESPs are often housed within complex piping systems or confined spaces, making physical access for inspection difficult
- Audibility and Visibility: Detecting small leaks can be challenging due to the limited audibility of sound waves and the visibility of potential leakage points
- Background Noise: The presence of ambient noise within industrial settings can mask the sound generated by air leaks, making detection even more complex
- Pressure Variations: Leaks might only become noticeable at specific pressure levels, making it tricky to detect them under varying operational conditions
- Multiple Leaks: In cases of multiple leaks, isolating individual leakage points from the cacophony of sounds becomes a daunting task
- Specialized Expertise: Detecting air leaks often requires trained personnel with expertise in ESP systems and leak detection techniques.
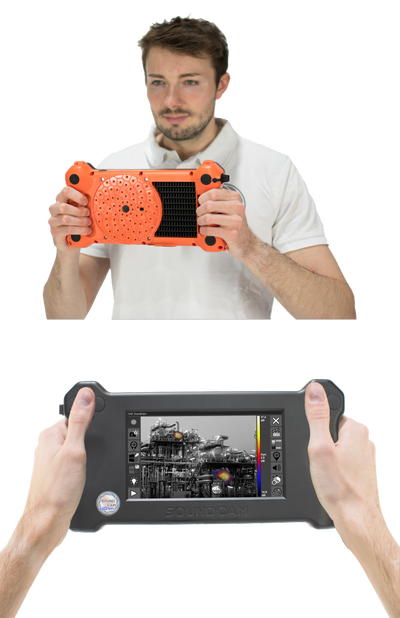
Simplifying Air Leak Detection with Ultrasound Acoustic Imaging Cameras
Acoem presents – Acoustic Camera SoundCam Ultra an accurate, reliable, easy to use and cost-effective acoustic based machine condition monitoring solution. The SoundCam Ultra is the first and smallest handheld camera that creates acoustic images from audible and ultrasound. It locates sound sources in real time and displays the results instantly on the screen and helps to analyze machine wear, defects assessment, detects compressed air/ gas leaks, partial discharges and corona testing.
How Does SoundCam Help ?
SoundCam scans large areas quickly and locates air leaks by listening to, recognizing, and analyzing the sounds they emit. The Camera is faster and far more sensitive and accurate than the human ear, combining both sonic and ultrasonic frequencies.
-
- Enables objective recordings and visual documentation, so that subjective assessments by individuals are avoided
- Portable small handheld device enables on the fly localization and perfect choice for small hard-to-reach spaces
- Captures high acoustic frame rates, crucial to clearly distinguish between different sounds
- Rugged and Ergonomically designed
- Instant analysis & diagnosis onsite with inbuilt software
- Sensitive to sound and ultrasound frequency ranges up to 100 kHz
- Detection of mechanical and electrical faults
- Integrated object lighting
- Easy to use diagnosis features with integrated touchscreen
- Detection from safe distance
Benefits of Using SoundCam Ultra
By integrating SoundCam Ultra into ESP maintenance, industries can unlock a range of benefits:
- Efficiency Boost: Prompt detection and repair of air leaks optimize ESP performance, ensuring efficient pollutant removal.
- Environmental Compliance: Identifying and rectifying leaks minimizes the release of pollutants into the environment, preventing regulatory violations.
- Energy Savings: Addressing air leaks promptly improves ESP efficiency, leading to reduced energy wastage and associated costs.
- Equipment Longevity: Timely leak repairs protect ESP components from wear and tear, prolonging the overall lifespan of the system.
- Maintenance Planning: Detecting leaks early allows for proactive maintenance scheduling, minimizing operational disruptions.
- Process Optimization: Leak detection provides an opportunity to evaluate overall ESP conditions, identify operational improvements, and enhance the entire process.
Overall, monitoring air leaks in an electrostatic precipitator offers multiple advantages, including improved efficiency, compliance with environmental regulations, energy savings, extended equipment lifespan, optimized maintenance, and process optimization. By actively managing air leaks, organizations can ensure the optimal performance of ESPs and minimize environmental impacts.
Acoem Solutions
Tailored for Air leak Detection
Acoem has developed a tailored approach to address the reliability challenges faced by the industry. By conducting thorough audits, predicting equipment failures, and implementing sustainable solutions with advanced technologies, Acoem helps industries and ports improve their operations.
Our expert team has years of experience working on different industries with exposure to local working conditions. This specialist knowledge combined with many years of experience has led us to offer comprehensive solutions and diagnostic services remotely as well as on-site.
Next Generation Reliability Solutions
A suite of IOT-driven ecosystem
Our predictive maintenance tools, powered by AI and utilizing wired or wireless sensors, IoT, augmented mechanics, machine learning, and data analytics, help anticipate problems before they occur. Schedule maintenance at the right time, receive alerts for potential issues, and enhance industrial productivity with certainty.