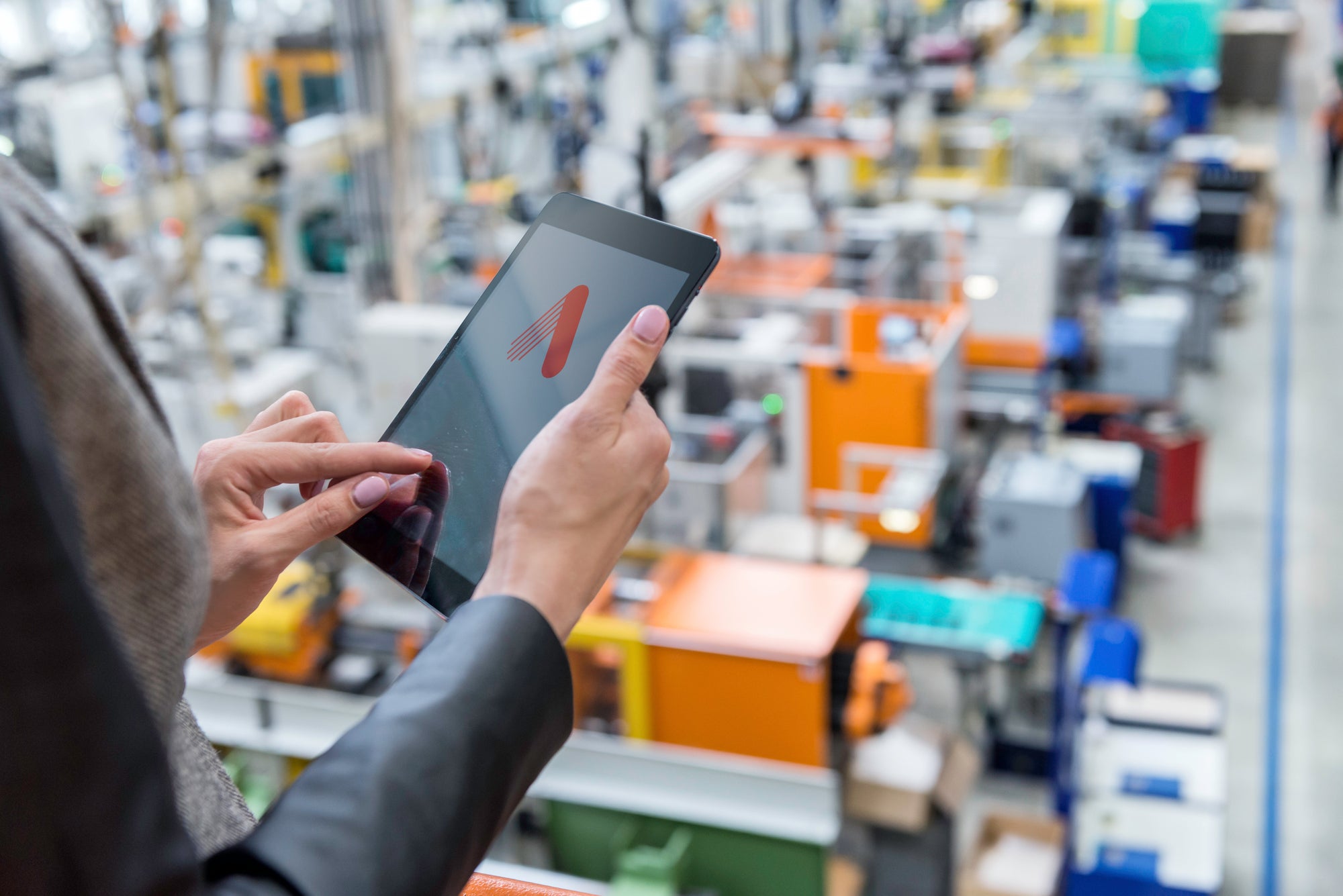
Online condition monitoring equipment
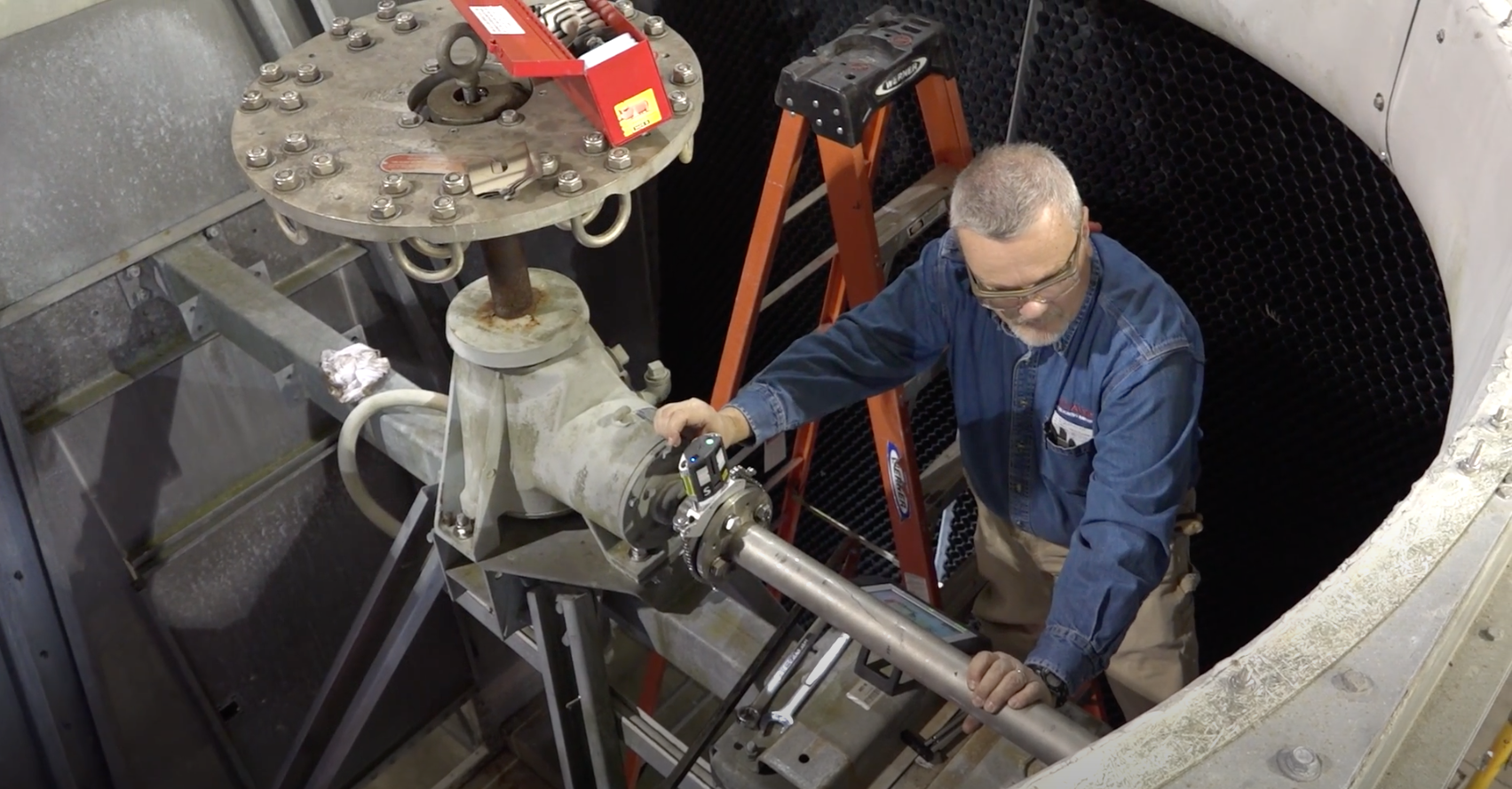
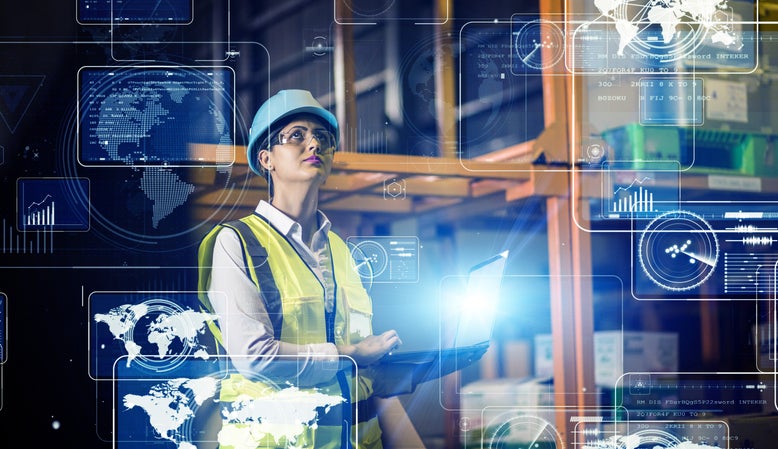
Acoem MV series online condition monitoring equipments
Acoem offers solution that can effectively monitor vibration levels of slow and variable speed bearings on even the most complex industrial machinery:
Suitable for a variety of industrial applications, both provide:
- Synchronous record of several rotations of low-speed shafts (<10RPM) can be performed on up 32 channels to improve bearing fault detection with the analysis of both low & high frequency content
- Acoem Shock Finder™, a smart algorithm developed on real applications that makes fault detection automatic & visible on any enabled device
- Up to 10 operating conditions that can defined by the operator using one or more process parameters
- Data acquisition strategy, indicators and alarm thresholds that are automatically adapted according to each operating condition
- Set stability parameters to ensure that each measurement is performed accurately
- Statistical analysis, band kurtosis & smart filters
- All post-processing indicators can be trended and help predict the evolution of the asset condition
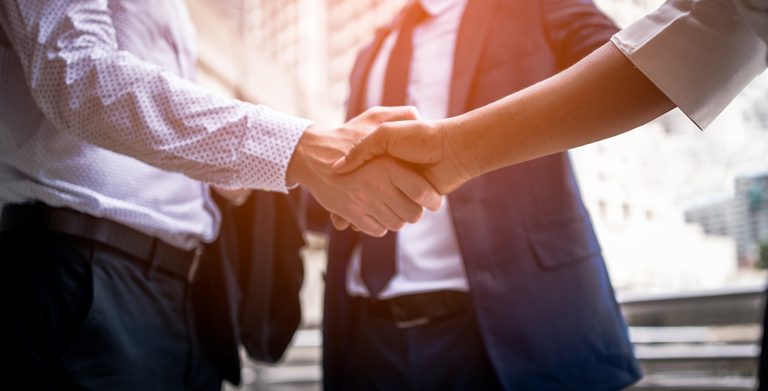
See it in action
Learn more or schedule a demo.