"We installed this wireless sensor a year ago, is it capturing any data?"
"If I had advanced notice, I could have ordered the right parts."
"We have all of this vibration data but nothing tells us what to do."
"Nobody told me that this machine was going to fail."
Meet Advisor
Advisor is a condition-based maintenance strategy that seamlessly integrates into an organization’s maintenance program to increase asset integrity and availability.
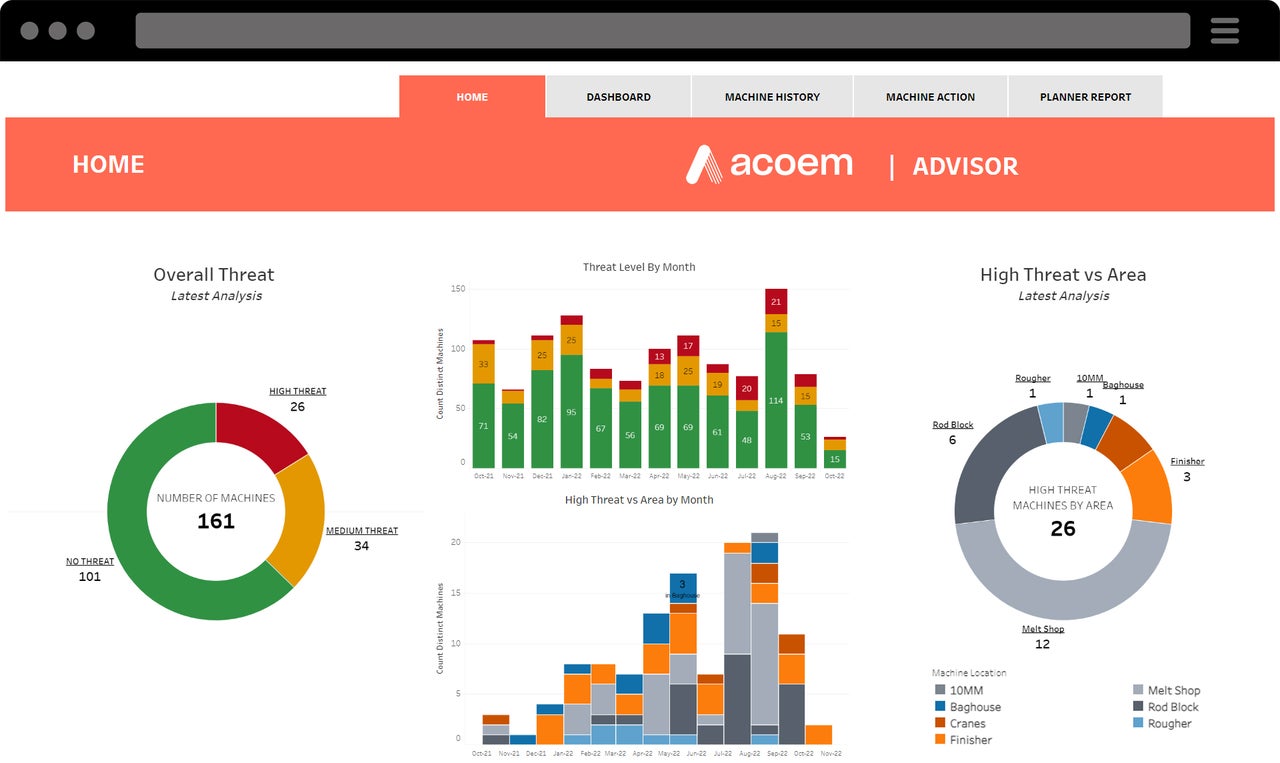
Hover over each step to learn more:
Data Collection
After we determine the most effective method of monitoring for each asset (handheld route-based, wireless sensors, and/or continuous monitoring), vibration data is collected.
Vibration Analysis
Once vibration data is collected, our remote team of level 3 and 4 vibration experts analyze the data and report findings within 24 hours.
Actionable Data
The results of each machinery analysis are immediately available to view in the Advisor Dashboard , our secure, web-based, data visualization tool. We advise on the how, what, and when to fix each problem.
Corrective Action
If machine faults are identified, maintenance becomes the next logical step. We will be by the client’s side throughout the process to help troubleshoot any roadblocks that are encountered.
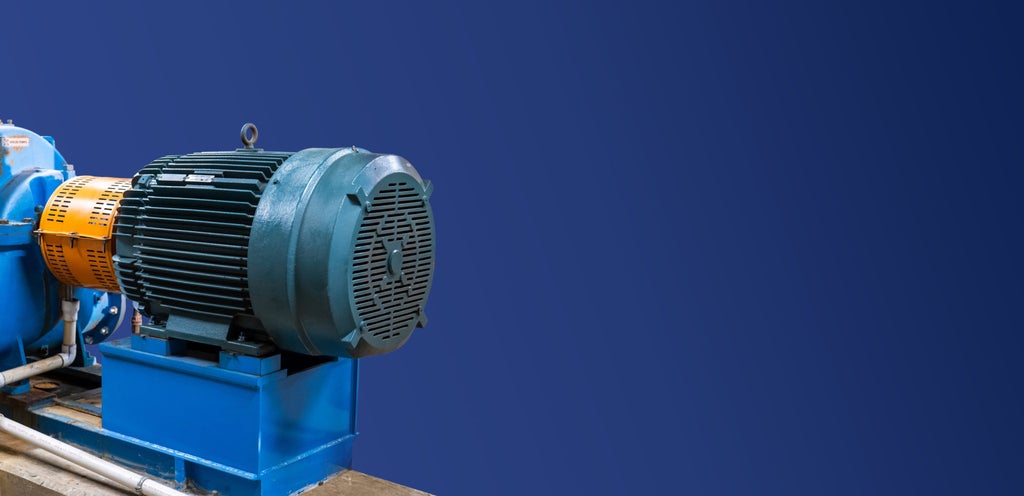
Working within your security protocols
- Some security protocols may prevent sensors from sending data to an external cloud. Or you may not wish for your data to be stored on Acoem servers.
- With Advisor, we send data to your specified location utilizing our Nest i4.0 Webportal to accommodate any restrictions in place.
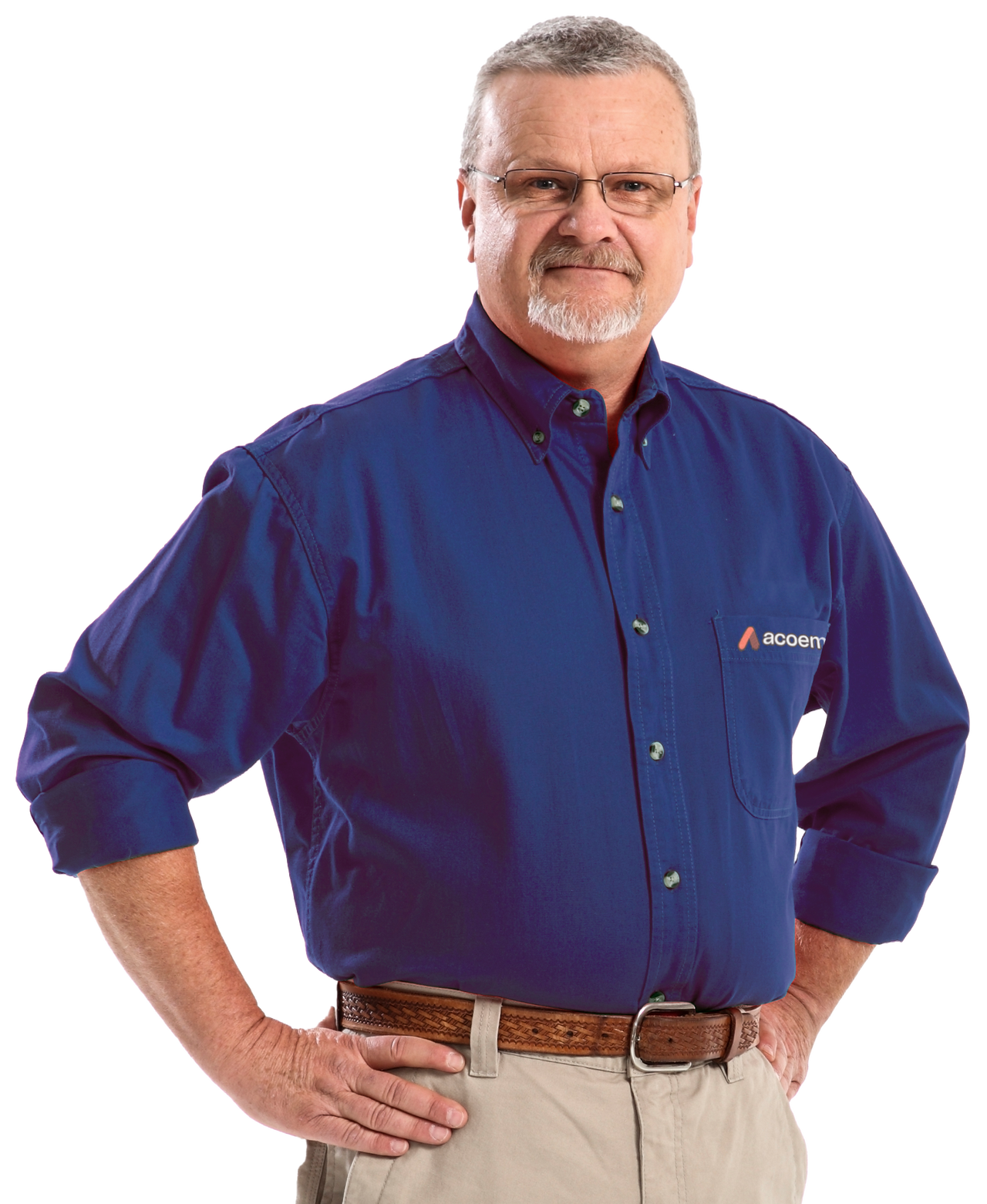
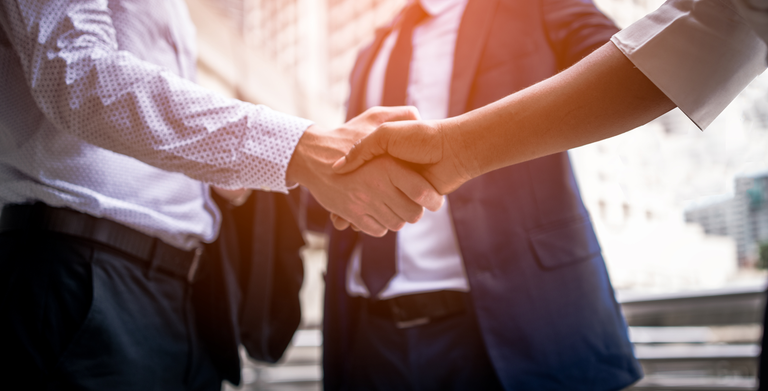
Want to learn more about Advisor?
Enter your contact information below and a machine expert will contact you within the next 24-48 hours.