Mechanical seals come in a multitude of designs that range from simple spring designs to more complex designs like cartridge seal types. Knowing how to care for, handle, clean, assemble, and install mechanical seals is instrumental in prolonging their life.
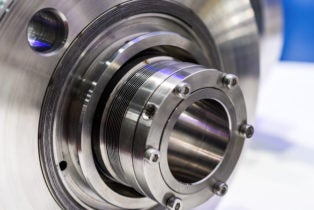
Proper Handling & Cleanliness
When handling a mechanical seal, treat it like a bearing. Most mechanical seals have instructions on the box with guidance on how to handle them, so it is recommended to consult those first. Always handle seals with clean hands, free of any grease or oil. Some seals are so fragile that bare hands cannot come in contact with them because the oils on our skin can damage them.
3 Best Practices
Below are 3 Best Practices to to make sure mechanical seals are handled with care:
- Use clean hands or gloves. (This is so important we had to repeat it again).
- Keep away from any dust, debris or lint.
- Never drop! If they are dropped, you will need to replace it.
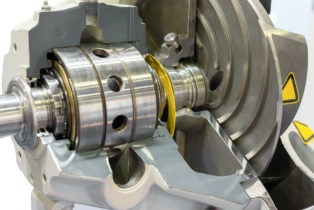
Installation/Assembly
Some mechanical seals require precise installation. Take Balanced and Unbalanced seals for instance, they have a spring and require pressure to be sealed. If the seals are not perfectly touching they will leak. So how can an installation go wrong?
1. Not following the installation instructions.
Mechanical seals can be easily damaged during installation and that’s why it is important to consult with the instructions that come with the packaging. For example, some instructions will advise that you remove spacers before starting the unit. If those spacers aren’t removed, then damage to the internal components could occur.
2. Installing on a misaligned pump.
Look, we get it, we’re in the business of alignments. If we weren’t telling you to align your machines, we wouldn’t be doing our jobs. A variety of issues can cause pump misalignment, including pipe strain, deflection during a hard start, shaft runout, and more. That’s why it is integral to make sure that your pump is properly aligned or you will damage your mechanical seal and have to do another installation.
3. Lack of or improper lubrication on the shaft.
Without the proper lubrication you can cause the o-rings on your mechanical seal to tear or roll which will permanently damage them. Despite having a variety of options, like petroleum jelly, silicone grease, or special lubricants, always consult the instructions to make sure the lubricant used is compatible with your seal as well as the product that will be pumped through. Mechanical seals are fragile and depending on the lubricant used, components can break down over time, therefore shortening the life of the seal.
4. Mishandling the seal.
We recommend that you never take a seal out of the packaging until it’s ready to be installed. Once you take it out of the packaging, do so with thoroughly washed hands or by wearing gloves. If you need to set it down, place it on a lint-free work towel or clean workbench to prevent contamination.
5. Uneven or over-tightening of fasteners.
This is easily the most common mistake, after cleanliness. Sometimes when a seal starts to leak, the first reaction is to tighten it, however, this often makes the problem worse. Instead, loosen the seal a bit, and see if the leakage is solved. Over-tightening fasteners can distort seal components and inevitably cause more leaking.
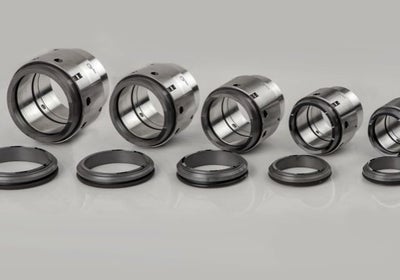
Lifespan
It depends on the seal and who you ask, but a mechanical seal could last anywhere between 2-10 years. When seals need to be replaced, they can be quite expensive, sometimes more than $1000 per inch of shaft diameter. As we’ve already covered, proper handling and cleanliness will help maximize the lifespan of your mechanical seal, but there are a few other variables to consider as well.
Depending on the liquid running through, the environment, or errors during installation, the following factors can impact how long a mechanical seal can last:
- Heat generations
- Letting a pump run dry
- Too much vibration
- Hammering couplings
- Using the wrong seal
We hope this helps you understand how to properly care for and avoid failure with mechanical seals.