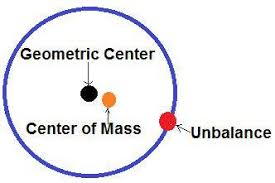
There are a few requirements to calculate a trial weight:
- You must know the speed of the machine. The faster the rotation, the more force from a trial weight.
- The radius of weight placement. The farther from the center of rotational mass, the more force.
- The weight of the rotor being balanced.
In many instances, a trial weight is calculated to generate a centrifugal force equal to 10% of the rotor’s weight. NOTE: Not 10% of rotor weight – 10% of the rotor’s centrifugal force. Also, if the rotor is operating above 3600 RPM, a calculation of 5% of the rotor’s weight is recommended.
To Calculate Centrifugal Force – Cƒ = mrω²
Where:
Cƒ = Centrifugal Force, in Lbf
m = Mass of the rotor (lb/386.4 in/sec²)
r = radius of weight placement
ω = Rotor speed in radians
Let’s try it in an example. We have a fan, running at 600 rpm, with a rotor weight of 400 lb., and we have an 18 radius of where the trial weights will be placed.
STEP 1
If we want a centrifugal force equal to 10% of the rotor, we use (.1 x 400 lb) = 40 lb.
STEP 2
Convert speed from RPM to Hz (600/60) = 10 Hz.
To get the speed in radians – (2π) (10 Hz) = 62.83 rad/sec
To get ω² – 62.83² = 3947.84 rad/sec²
So:
m= _____ 40 lb _____ = 0.00056
___(18”)(3947.84 rad/sec)
Now that we have the mass, we need to calculate for the weight – W=mg
m=0.00056
g=386.4 in/sec²
W=(0.00056)(386.4)=0.217 lb or (.217)(16 oz in a pound) = 3.472 oz
A Simplified Calculation
Trial weight = 56375.5 x rotor weight
_______________RPM² x radius
______________56375.5 x 400 lb = 3.478 oz.
_______________600rpm² x 18”
Knowing the speed of the machine and the radius of weight placement is easy. What was typically more difficult for me was knowing the rotor weight. If you can find it, the simplified calculation formula works well. If you feel comfortable in estimating it, just be careful, and lean toward the light side. FYI-steel weighs about 500 pounds per cubic foot.
If you keep records on balancing rotors (and your probably should), you can often calculate a good trial weight by knowing the previous balance job.
As an example:
On a previous balance, the fan in question had vibration at 0.42 in/sec at 1xrpm. Balancing correction required 3.5 oz of weight, which reduced the vibration to 0.036 in/sec.
3.5 oz. = 9.114 oz/in/sec
.42 in/sec – 0.036 in/sec
If the new unbalance is .4 in/sec
.4 x 9.114 oz/in/sec = 5.468 oz to balance. I typically use 50% of this as a trial weight.
Remember, this assumes there have been no changes made to the rotor since the previous balance. If the rotor is dirty, it is different, and should probably be cleaned before attempting balancing.