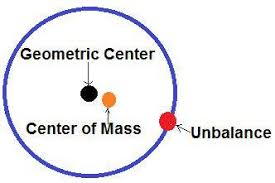
If you have no balancing record
If you have no balancing record for this rotor, where to place the weight is little more than a guess. But there are some things you can do to improve your chances of placing the trial weight in a good location:
- Look for places where a correction weight might have fallen off. A shiny place on an otherwise dull fan finish. A weld bead that seems out of place, or not attached to anything.
- Mark the top of the rotor with a marker, and roll it over 90 degrees or so. If it rolls back and places the marked location back near the top, it’s a good guess that your mark is near the light spot. If it’s a belt-driven rotor, you might want to remove the belts, which will make it roll the heavy spot down a little more easily.
If you don’t have any clues
If you don’t have any clues where the light spot may be, then placing the trial weight is just a guess.
Some very important things to determine:
- Does your balancing machine measure rotation with, or against rotation?
- Determine whether to place the weight on the leading, or trailing edge of the blade. Use common sense here. You want the centrifugal force to work with weight-to minimize the risk of it coming loose. In this example, you want to place the weight on the leading edge of the blade.
- You must determine angular position where weights may be placed. If weights can go on any place around the rotor, you can use 360°, or clock positions. In our example, we have 8 blades, so there are 8 places where a weight can be placed. You can divide this into 45° increments, or on most modern balancing machines (such as the Fixturlaser SMC, or OneProd Falcon), you can input the number of locations.
- It is good practice to use a marker, and number the blades or locations, consecutively:-With rotation (if your machine balances with rotation), or-Against rotation, if that’s how your machine works.
- You should also determine the radius of where the weights will be mounted. The farther away from the center of rotation, the more effect the trial weight will have. Again, a good trick is to slow roll the rotor, and hold the marker against the rotor, “drawing” a circle where weights should be placed.
- If the rotor had a bolted hub (like the one in this photo), you may find it beneficial to use washers, and place them under the bolts, as opposed to clamping weights on the blades themselves. This is especially true if the blades are thin and could be damaged by clamping a weight on the blade. If the blades are fiberglass, always use the hub for balancing weights.
- Speaking of weights, it is recommended that trial weights be easily moveable, and removable. Some companies sell “bolt-on” weights, or you can make your own. I have used putty (if it will stay in place), lead tire weights (with two-sided tape), washers, and so on. A correction weight should be affixed to stay for good, i.e. bolting or welding. A bolt on trial weight can be welded on, but I would not recommend it until you KNOW that the weight is in the right place, and is the right amount, to correct the unbalance.
A few other tips:
- Record your balancing steps, locations of weights, and even where the vibration sensor and laser tachometer are mounted, as well as where the reflective tape is located. If you ever have to re-balance this rotor, you’ll have a good head start.
- If the rotor has several weights, placed in various places all over the rotor, you might consider removing them all, and starting over from scratch.
- If you install the trial weight, and the vibration goes up-it’s OK. But if it goes up too much, you may consider moving the trial weight 180 degrees, and re-measuring the trial run. Moving the trial weight 180 degrees should make the vibration decrease proportionally.
- Speaking of proportional, balancing should be a logical and proportional process. If several trial runs are tried, and nothing seems to make the unbalance better, your problem probably isn’t unbalance. Look for other problems that can cause vibration at 1x running speed, such as looseness, broken welds, etc.