Having the necessary skills and knowledge is critical to ensuring that we are able to keep these essential services available. Understanding the root causes of machinery failure will help us to avoid unscheduled downtime and interruption of these services.
Your machines may be noisy, running hot, excessively vibrating, cavitating, or have dark looking oil. These conditions are symptoms of a deeper root cause. You can repair, replace, rebuild or remove symptoms and still not get rid of the root cause. The root cause is the fundamental or main reason for the failure.
Root causes can be issues like imbalance, misalignment, poor lubrication, resonance, particle contamination, moisture contamination, soft foot or many other types of problems. Think about these differences in symptoms and root causes like a weed. You can keep cutting a weed, but it typically grows back again and you have to cut it again. If you take the time to pull the weed out with all its roots and hopefully you never have to deal with it again.
Preventing root causes is also much cheaper than removing the root causes once they are in place. Let’s look at some ways that we can prevent root causes for failures in lubrication vs. ways of removing them.
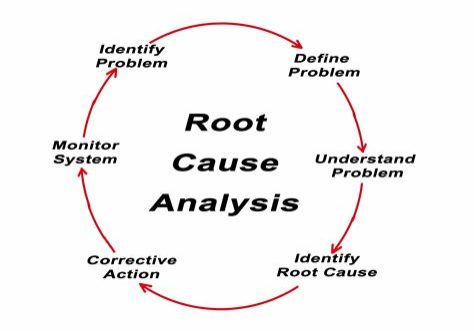
Lubricant contaminant exclusion = Cheaper
- Filter new oil
- Use good quality breathers
- Use proper lubrication application methods
- Upgrade seals
- Use hydraulic cylinder rod boots
Lubricant contaminant removal = Expensive
- Upgrade system filters
- Vacuum dehydration
- Centrifugal separation
- System flushing
- Water absorbing filters
Having a well-trained maintenance staff who is equipped with the right tools and knowledge can help keep the root causes of machinery failures eliminated or at least to a minimum. Here at Acoem, we have a passion for training and sharing information. Let us help equip you with the tools and training to assist you on the road to reliability!