Economic profitability
The first aspect to take into consideration is the economic profitability, such as the ratio between the cost of the risk incurred and that of the monitoring system put in place to avoid this risk. Without this economic constraint, the answer to the question “How many sensors?” would simply be: as many as necessary to check all the critical components. We always start by quantifying the risk (acceptable and unacceptable) in order to define the budget with which we will work. It goes without saying that this budget varies depending on the size of the gearbox, not least because of the costs and the supply time for components.
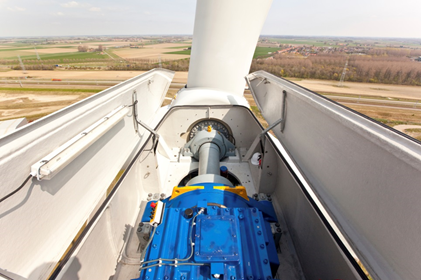
Number of sensors
From this budget, we decide the number of sensors that we will put in place with the objective of finding the right balance between “over-instrumentation” (unnecessary costs) and on the contrary, “under-instrumentation” (too much residual risk). At this stage, it is the predictive maintenance strategy which comes into play, namely the level of accuracy that is expected in the diagnosis. For example, on a shaft equipped with a bearing at each end, one sensor can identify a problem, but 2 sensors will help locate the problem as well as help target the operation.
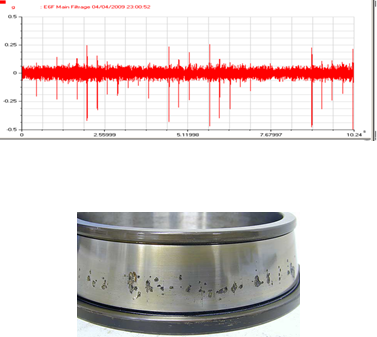
Sensors’s installation
Once the number of sensors has been determined, all that remains is to decide where to install them. In this last phase, we are guided by two main principles: the distance to the source of the problem and the direction of internal efforts. We always seek to place our sensors as close as possible to the bearing or gear to be monitored. The further away we are from it, the more we have to filter the vibration signal in order to have a clear view of the defect. When the defect is not important enough to generate vibrations throughout the structure, it becomes, from afar, almost impossible to see. We also always seek to position ourselves in the direction of propagation of the default signal which depends on the direction of the internal efforts. For example, for straight gears we will seek to use radial sensors, whereas for helical gears, it will be necessary to use both an axial sensor and a radial sensor in order to see the big picture.
As you will have understood, the decision of where to put the sensors is somewhat akin to a “triangulation” in which we seek to capture the “enemy” signal and determine as precisely as possible its location.