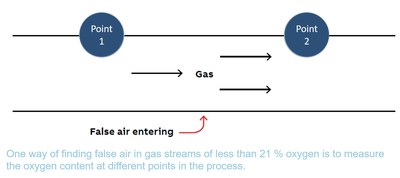
What is false air
False air is any unwanted air entering into the process system. The exact amount of false air is difficult to measure. However, an indicator of false air can be, increase of % of oxygen between two points (usable for gas stream containing less than 21 per cent of oxygen). Due to unwanted air, the power consumption increases and system’s temperature decreases. Therefore, to maintain the same temperature fuel consumption has to be increased.
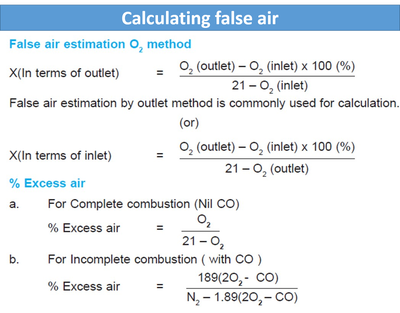
Energy contributes to almost 40% of the cost of production and hence energy conservation assumes greater importance as one of the best ways for improving productivity.
Impact of false air in cement plant:
- Increase of power consumption
- Increase the fuel consumption
- Unstable operation
- Reduction in productivity
- Higher wear of fans
- Drop of temperature for drying raw material
- Difficulty to transport material
False air intrusion points
Generally false air intrudes in kiln section through
- Kiln outlet
- Inlet seal
- TAD slide gate
- Inspection doors and flap box
In mill section false air intrudes through
- Rotary feeder at mill inlet
- Mill body
- Mill door
- Flaps
- Expansion joints
- Holes of ducts and tie rod entry point
In power sector, as margin is very less, cost- effectiveness plays an important role. Generally false air intrudes in CPP section through
- Air pre-heater casing
- Boiler main door
- Fan casing,
- Inspection doors
- ESP main doors
- ESP hopper doors
- Expansion bellows and ducts
In GPP section false air intrudes through
- Main holes
- Hammering
- Bellows
- Rotary air locks
- Damper casing
- Expansion bellow, etc
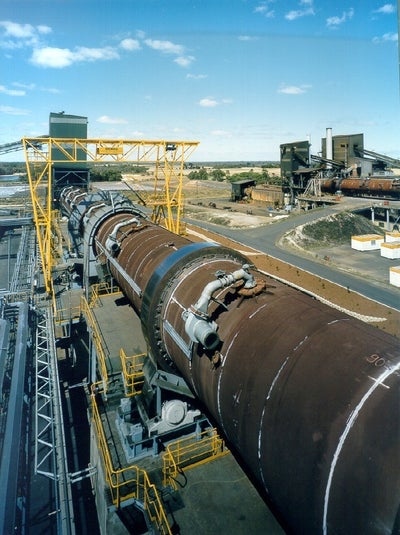
False air detection through ultrasonic leak detector
Ultrasonic leak detectors often called sniffer, especially designed to find small leaks, are also being used in enclosed gas systems. Since ultrasonic gas detectors search for the sounds of leaks rather than escaping gases, they are able to detect leaks of any gas type. Though the device is unable to measure gas concentration, it is able to determine the leak rate of an escaping gas because the ultrasonic sound level depends on the gas pressure and size of the leak. When gas escapes a pressurized line, it generates a sound in the range of 25 kHz to 10 MHz, well above the frequencies the human ear is sensitive to but in a range easily identifiable to ultrasonic sensors. When the detector senses ultrasonic frequencies, they are isolated from normal background noise, amplified, and converted to a frequency audible to humans.
Detection principle: When a gas passes through a restricted orifice under pressure, it goes from a pressurized laminar flow to low pressure turbulent flow. The turbulence generates a broad spectrum of sound called “white noise”. There are ultrasonic components in this white noise. Since the ultrasound is loudest at the leak site, it can be detected very easily.
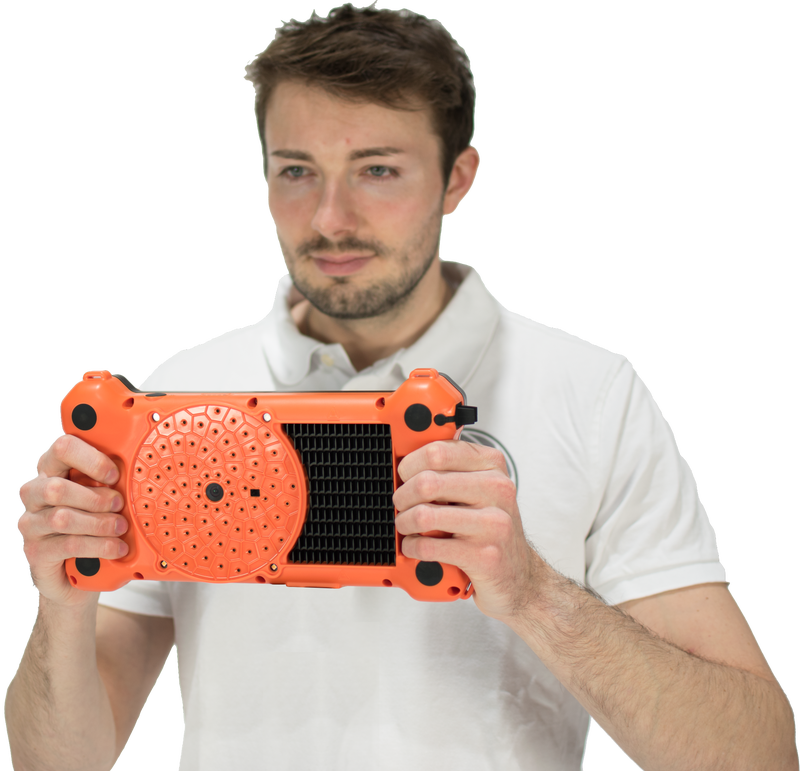
Acoustic based condition monitoring is the future of predictive maintenance.
Together with machine learning and advanced signal processing, impending machine failures can be detected and tackled ahead of time.
Acoem presents – Acoustic Camera SoundCam Ultra an accurate, reliable, easy to use and cost-effective acoustic based machine condition monitoring solution. The SoundCam Ultra is the first and smallest handheld camera that creates acoustic images from audible as well as the ultrasound range. It locates sound sources in real time and displays the results instantly on the screen and helps to analyse machine wear, gives defect assessment, detects compressed air/ gas leaks, partial discharges and corona testing.