Figure 3.1 The dial indicator
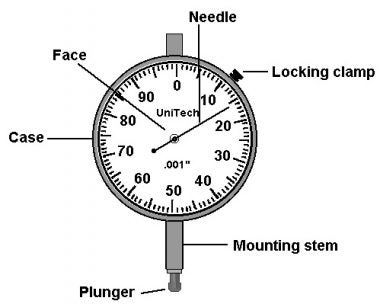
Figure 3.2 Dial indicator signs
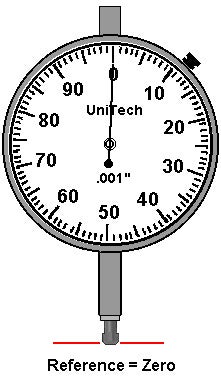
Figure 3.3 Positive readings when the plunger moves into the case, negative when the plunger moves out.
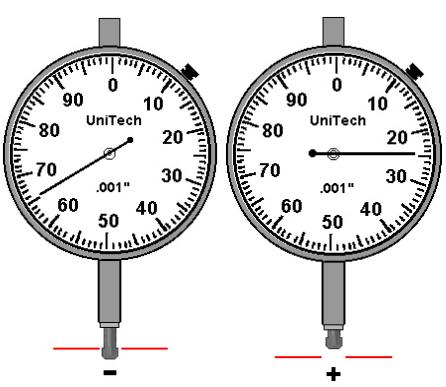
Figure 3.4 Determining bar sag, zero at 12 o’clock.
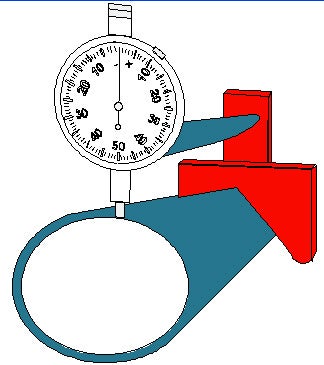
Figure 3.5 Determining bar sag, reading at 6 o’clock.
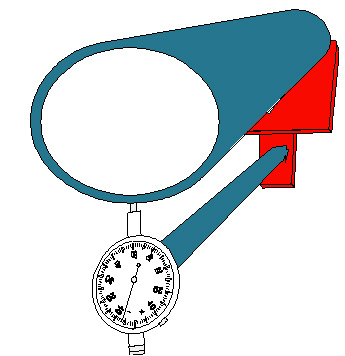
Figure 3.6 Measuring offset, position #1.
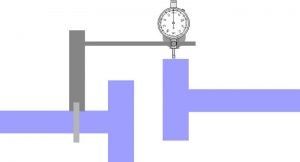
Figure 3.7 Measuring offset, position #2.
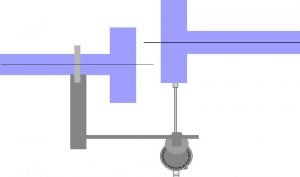
Figure 5.8 The offset is half the TIR (Total Indicator Reading).
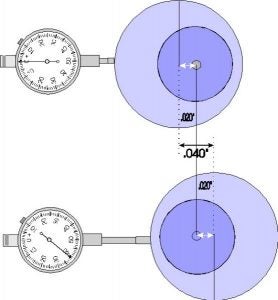
Figure 3.9 Measuring angularity, position #1.
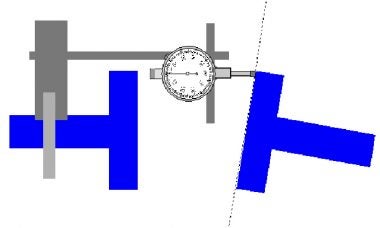
Figure 3.10 Measuring angularity, position #2.
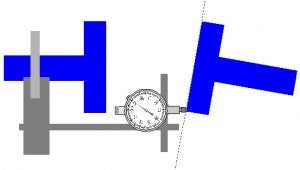