Figura 3.1 O indicador de discagem
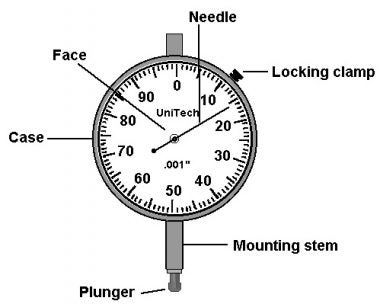
Figura 3.2 Sinais indicadores de discagem
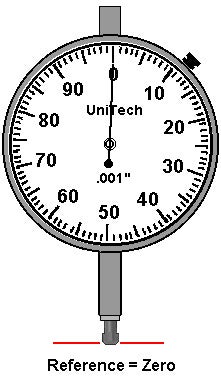
Figura 3.3 Leituras positivas quando o êmbolo se move para dentro da caixa, negativas quando o êmbolo se move para fora.
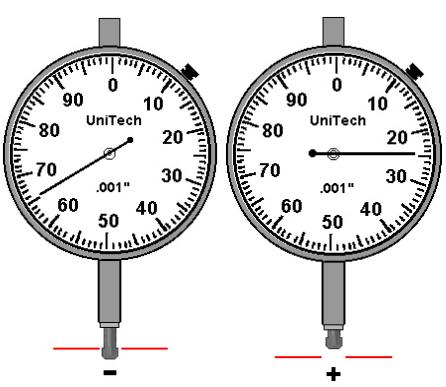
Figura 3.4 Determinação da inclinação da barra, zero às 12 horas.
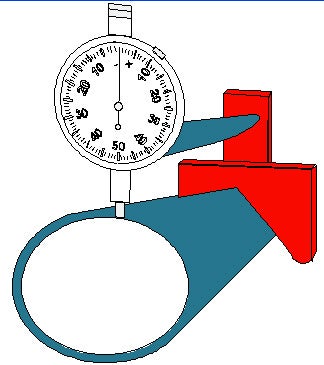
Figura 3.5 Determinação da inclinação da barra, leitura às 6 horas.
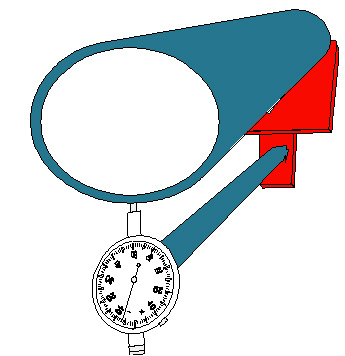
Figura 3.6 Offset de medição, posição nº 1.
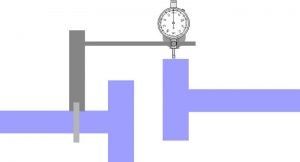
Figura 3.7 Offset de medição, posição nº 2.
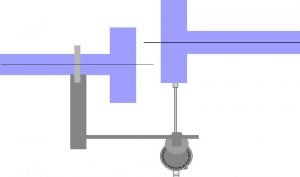
Figura 5.8 O
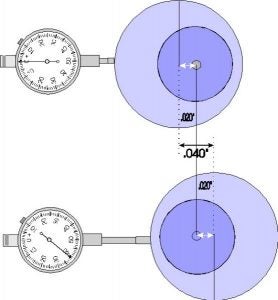
Figura 3.9 Medição da angularidade, posição nº 1.
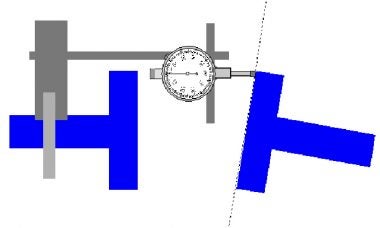
Figura 3.10 Medição da angularidade, posição nº 2.
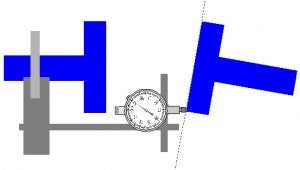